Les matériaux composites modernes ont permis de fabriquer indépendamment des pièces en plastique, de leurs propres mains.
Aujourd'hui, nous allons apprendre à mouler des pièces en plastique à la maison.
Contenu:
- Un peu sur la technologie de coulée à la maison
- Procédé de fabrication d'ébauche en plastique
- Étape numéro 1 - préparation du polyuréthane
- Étape 2 - Préparation du moule d'injection
- Étape numéro 3 - fixation du moule d'injection sur le substrat
- Étape 4 - entonnoir de coulée
- Étape numéro 5 - préparation de la composition de polyuréthane
- Étape numéro 6 - mélanger les réactifs
- Étape numéro 7 - casting
- Étape 8 - retirer le produit du moule
- Résultat et résumé
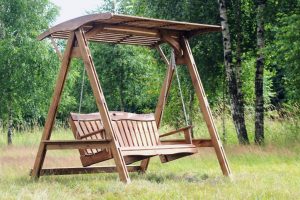
Un peu sur la technologie de coulée à la maison
Pour la fabrication de produits en plastique, une certaine préparation sera nécessaire - il est nécessaire de fabriquer une matrice en silicone, ainsi qu'un substrat de comptoir à partir du même matériau.
Les moules de coulée sont fabriqués en silicone Elastolux de haute qualité. Ils prennent comme source les modèles maîtres réalisés sur une imprimante 3D, ou le modèle original de la production industrielle.
Les substrats sont généralement fabriqués à partir de matériaux en silicone moins chers, tels que l'Elastoform.
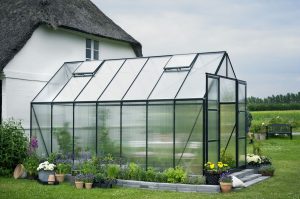
Procédé de fabrication d'ébauche en plastique
Nous utiliserons le polyuréthane à deux composants "Unikast 9" comme matériau de coulée, composé du polyuréthane lui-même et du durcisseur.
Le prix d'un pack de ce consommable en magasin est d'environ 900 roubles, où environ 0,5 kg de base et 0,3 de durcisseur.
Étape numéro 1 - préparation du polyuréthane
Étant donné que le produit nécessite une couleur foncée, vous devez d'abord ajouter de la couleur à la base. Il est vendu séparément. Environ 100 gouttes sont nécessaires pour un paquet d'Unikast 9 - pour une couleur bleu foncé.
Pour que les nuances des produits ne diffèrent pas, la couleur doit être ajoutée à tout le volume de la base en polyuréthane.
Étape 2 - Préparation du moule d'injection
Le moule en silicone doit être préparé avant de commencer le travail - traitez-le avec un séparateur. Pour ce rôle, les mélanges de vaseline et les séparateurs à base de kérosène sont parfaits.
Étape numéro 3 - fixation du moule d'injection sur le substrat
Puisqu'un substrat du même matériau est utilisé comme base pour le moule en silicone, ils s'emboîtent parfaitement. Cependant, afin d'éliminer complètement les taches de la solution, vous devez appuyer le moule contre le substrat en silicone avec une charge supplémentaire.
Étape 4 - entonnoir de coulée
Nous fabriquons un entonnoir jetable en papier et l'insérons dans la carotte du moule.
Étape numéro 5 - préparation de la composition de polyuréthane
Pour cela, il est préférable d'utiliser des balances électroniques précises.
Nous plaçons un récipient en plastique sur la balance et réinitialisons cette dernière.
Versez la quantité requise de base de polyuréthane - pour chaque forme, le volume est calculé séparément.
On ajoute un durcisseur à raison de 0,6 pour 1. C'est à dire. 20 grammes de base nécessitent 12 grammes de durcisseur.
Étape numéro 6 - mélanger les réactifs
Remuez pas plus de 30 secondes une réaction chimique commence rapidement, comme en témoigne l'échauffement du mélange.
Étape numéro 7 - casting
Verser le contenu du récipient dans la matrice silicone.
Étape 8 - retirer le produit du moule
Après 20 minutes, vous pouvez retirer le produit en plastique.
Pour ce faire, retirez l'entonnoir avec l'excès de plastique congelé et sélectionnez les «jambes» en plastique des carottes.
Nous sortons le produit fini du moule.
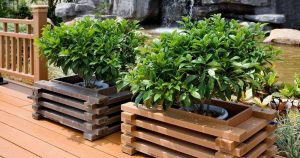
Résultat et résumé
Le produit s'est avéré être d'excellente qualité, l'ensemble du processus a pris environ 30 minutes. Il ne reste plus qu'à modifier légèrement la pièce: couper les pattes des carottes, nettoyer un peu le produit avec du papier de verre.
Si l'on compare cette technique de fabrication de produits en plastique avec l'impression 3D, on peut dire avec certitude que le moulage gagne en vitesse de production : 1 pièce en 30 minutes contre 4 heures. Quant au coût des matières premières, l'impression 3D est 3 à 3,5 fois plus chère.
Vidéo en vedette : FLOAT CASTING - Moulage de plastique en silicone
FLOAT CASTING - Moulage de plastique en silicone
Fabriquer des pièces en plastique à la maison ???